Stupid Question...
- JETTYWOLF
- Contributor/donator/Location Nazi
- Posts: 6074
- Joined: Sun Jan 06, 2008 9:11 pm
- 16
- Your location: JACKSONVILLE FL USA
- Location: Tree-hugger, USA...they call it FLA.
Stupid Question...
Since I'm here, I'll ask.
I see a boat and the aluminum is ".100 gauge" so what the hell does that mean. Are we talking 1/8th inch???
http://alweld.com/escort_bay_boat.html
I see a boat and the aluminum is ".100 gauge" so what the hell does that mean. Are we talking 1/8th inch???
http://alweld.com/escort_bay_boat.html
- goatram
- Donator 08, 09, 10, 11, 12, 13, 14, 15, 16, 17, 18, 19
- Posts: 1959
- Joined: Wed Apr 09, 2008 11:53 pm
- 16
- Your location: Stanwood, Wa
- Location: Stanwood WA
Re: Stupid Question...
No 1/8" is .125" .100 is a 1/10"
You having a good day Dave? it's 10pm and in another hour I will get to go home for the night

You having a good day Dave? it's 10pm and in another hour I will get to go home for the night

John Risser aka goatram
33' RBW with twin 250 Hondas (Aliens)
2015 Ford F350 Dually
Master of R&D aka Ripoff and Duplicate
33' RBW with twin 250 Hondas (Aliens)
2015 Ford F350 Dually
Master of R&D aka Ripoff and Duplicate
- welder
- Site Admin
- Posts: 4668
- Joined: Thu Jan 03, 2008 11:51 pm
- 16
- Location: Whitesboro, Texas
- Contact:
Re: Stupid Question...
.100 = 100/1000's and 1000 = 1"
so
.125 is VERY close to 1/8Th of a inch, there is 1 or 2 thousandths lost in the conversion.
so .100 being .025 [or 25/1000's ] smaller than .125 its going to be smaller or thinner you might say than 1/8 of a inch.
so
.125 is VERY close to 1/8Th of a inch, there is 1 or 2 thousandths lost in the conversion.
so .100 being .025 [or 25/1000's ] smaller than .125 its going to be smaller or thinner you might say than 1/8 of a inch.
Lester,
PacificV2325, Honda BF225
2386
PacificV2325, Honda BF225
2386
- goatram
- Donator 08, 09, 10, 11, 12, 13, 14, 15, 16, 17, 18, 19
- Posts: 1959
- Joined: Wed Apr 09, 2008 11:53 pm
- 16
- Your location: Stanwood, Wa
- Location: Stanwood WA
Re: Stupid Question...
Dave you confused yet 

John Risser aka goatram
33' RBW with twin 250 Hondas (Aliens)
2015 Ford F350 Dually
Master of R&D aka Ripoff and Duplicate
33' RBW with twin 250 Hondas (Aliens)
2015 Ford F350 Dually
Master of R&D aka Ripoff and Duplicate
-
- Donator '09
- Posts: 2246
- Joined: Sun Jan 13, 2008 12:19 am
- 16
- Your location: Seattle, WA
- Location: Seattle, WA
Re: Stupid Question...
Hey, those guys aren't on the big builder list, thanks for the tip Dave.
BTW, its a "tinny", Dave
BTW, its a "tinny", Dave
1987 24' LaConner pilothouse workboat, 225 Suzuki

please view and like: https://www.facebook.com/bottompainting/

please view and like: https://www.facebook.com/bottompainting/
- JETTYWOLF
- Contributor/donator/Location Nazi
- Posts: 6074
- Joined: Sun Jan 06, 2008 9:11 pm
- 16
- Your location: JACKSONVILLE FL USA
- Location: Tree-hugger, USA...they call it FLA.
Re: Stupid Question...
DAMN..........
I was showing that boat to my "Jetty pup".
My prodigy. A young 27 year old ex-Marine that I've taken under my wing, over a year ago. Who just sold his 18' Century CC boat, for exactly what he paid for it a year ago, on Craigs List.
I'd like to see him "slide" into a aluminum boat that he can tow behind his small SUV, with a "entry cost" is relativly low. A simple boat that would work for him, in our river and at the inlet jetties. That hull bottom looked nice and the layout was not manufacture designed. Where you have to live with crap they decided you need....like 99% of all plastic boats have.
But less than an 1/8th inch????
That's what their web site says the boat is. Not the very bottom too???? really????
Geez, my BLM/Pacific sure has spoiled me. It's such a damn tank!
Oh well, I requested a "QUOTE" on their web site days ago and they've failed to e-mail me back.
And if that's how they like to NOT sell boats. I guess I'll tell him to forget about that hull.
ALWELD boats.......yer messing up already! Ya need to tighten up!


I was showing that boat to my "Jetty pup".
My prodigy. A young 27 year old ex-Marine that I've taken under my wing, over a year ago. Who just sold his 18' Century CC boat, for exactly what he paid for it a year ago, on Craigs List.
I'd like to see him "slide" into a aluminum boat that he can tow behind his small SUV, with a "entry cost" is relativly low. A simple boat that would work for him, in our river and at the inlet jetties. That hull bottom looked nice and the layout was not manufacture designed. Where you have to live with crap they decided you need....like 99% of all plastic boats have.
But less than an 1/8th inch????
That's what their web site says the boat is. Not the very bottom too???? really????
Geez, my BLM/Pacific sure has spoiled me. It's such a damn tank!
Oh well, I requested a "QUOTE" on their web site days ago and they've failed to e-mail me back.
And if that's how they like to NOT sell boats. I guess I'll tell him to forget about that hull.
ALWELD boats.......yer messing up already! Ya need to tighten up!

-
- Donator '09
- Posts: 2246
- Joined: Sun Jan 13, 2008 12:19 am
- 16
- Your location: Seattle, WA
- Location: Seattle, WA
Re: Stupid Question...
Its kind of an interesting hull as sheet boats go . . . interesting chine but if you look closely the boat looks like its made out of pressed aluminum foil. Its 100% welded though so they're giving it the old college try . . .


1987 24' LaConner pilothouse workboat, 225 Suzuki

please view and like: https://www.facebook.com/bottompainting/

please view and like: https://www.facebook.com/bottompainting/
- JETTYWOLF
- Contributor/donator/Location Nazi
- Posts: 6074
- Joined: Sun Jan 06, 2008 9:11 pm
- 16
- Your location: JACKSONVILLE FL USA
- Location: Tree-hugger, USA...they call it FLA.
Re: Stupid Question...
Yeah, I wasn't all that impressed with that particular photo either. And I think it may have lost something in the process of making it that way for the website.
I dad see a 16' duck boat of theirs and it was pretty nicely made. So when I saw a 21 or 23 foot skiff like this I thought maybe this would be good for my Jetty-pup guy.
In today's world, I don't see how any company doesn't jump to communicate with even a far off potential customer.
I'd still like to at least see that boat in either the 21 or 23 (WOW) version. I say wow because that's kinda big for less than an 1/8th inch aluminum and capable of hanging a 200 on the back.
I dad see a 16' duck boat of theirs and it was pretty nicely made. So when I saw a 21 or 23 foot skiff like this I thought maybe this would be good for my Jetty-pup guy.
In today's world, I don't see how any company doesn't jump to communicate with even a far off potential customer.
I'd still like to at least see that boat in either the 21 or 23 (WOW) version. I say wow because that's kinda big for less than an 1/8th inch aluminum and capable of hanging a 200 on the back.
Re: Stupid Question...
I don't feel secure unless the bottom is at least 3/16" (that's .1875" for you Dave). A good bottom is 1/4". Especially if the boat is going to slide over a rocky bottom.
-
- WON Super Star Donator '08, '09, '10, '11
- Posts: 638
- Joined: Sat Mar 15, 2008 1:07 pm
- 16
- Location: So. Calif.
Re: Stupid Question...
Looks to be a similar build as the Bayrunners
Do the specs look kind of similar?
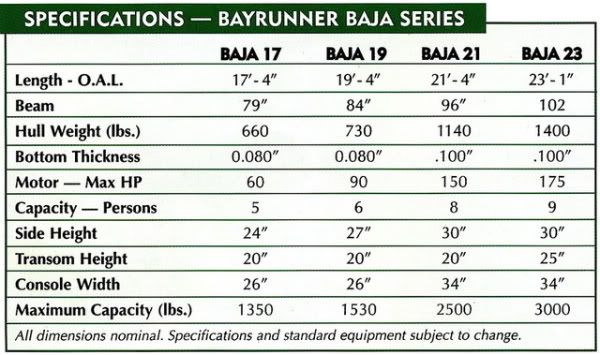
I'm thinking that the ribs are press formed to increase the stiffness and then the chines are welded to the bottom of the hull.
Bayrunners were very affordable in the height of their popularity but I think the cost to manufacture them made them less affordable.
Jettywolf, let us know the prices of those Alwelds
Alwelds are tough enough to wrangle these bad boys

Can't say I'm a watcher of this show (Swamp People) since I don't have cable or satellite TV but I've heard stories about it
http://www.history.com/shows/swamp-people
Might be the life for Jetty
Lower rent
Everything you'll ever need right in your front yard
No salt to corrode the Honda
"Livin' off the fat of the land"

Do the specs look kind of similar?
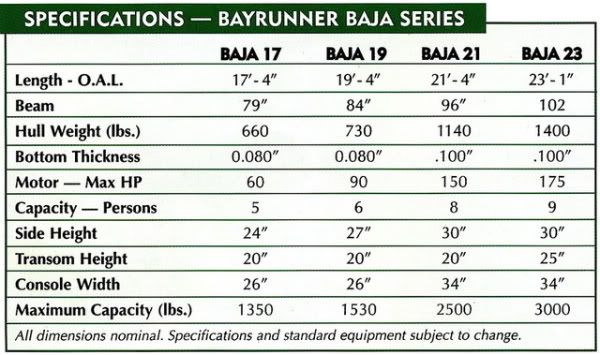
I'm thinking that the ribs are press formed to increase the stiffness and then the chines are welded to the bottom of the hull.
Bayrunners were very affordable in the height of their popularity but I think the cost to manufacture them made them less affordable.
Jettywolf, let us know the prices of those Alwelds
Alwelds are tough enough to wrangle these bad boys

Can't say I'm a watcher of this show (Swamp People) since I don't have cable or satellite TV but I've heard stories about it
http://www.history.com/shows/swamp-people
Might be the life for Jetty
Lower rent
Everything you'll ever need right in your front yard
No salt to corrode the Honda
"Livin' off the fat of the land"

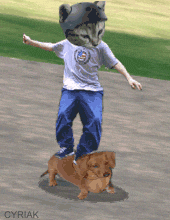
1989 22' Walkaround Cuddy Bayrunner
2001 115 Merc. 4 stroke/1988 9.9 Yamaha 4 stroke kicker
- JETTYWOLF
- Contributor/donator/Location Nazi
- Posts: 6074
- Joined: Sun Jan 06, 2008 9:11 pm
- 16
- Your location: JACKSONVILLE FL USA
- Location: Tree-hugger, USA...they call it FLA.
Re: Stupid Question...
Yeah specs are similar, but the Baja's are call "Bay Boats" round here. Just a styling thang.
Man that Alweld would be great if it was at least 3/16th thru-out.
Man that Alweld would be great if it was at least 3/16th thru-out.
Re: Stupid Question...
Weld built,allweld,both use 100guage .. Very tough boats .. I’ve had two and just bought my third .. Keep going bigger each time .. Southfork and sea Ark use 125 and are beast .. But prices are as well ..
-
- Donator 08, 09, 10, 11, 12, 13, 14, 15, 16, 17, 18, 19, 20, 21, 22, 23, 24
- Posts: 1745
- Joined: Mon Aug 18, 2008 1:37 am
- 15
- Your location: Kenai, AK
- Location: Kenai, Alaska
Re: Stupid Question...
Forum, I realize the dimension or scantling being discussed in the OP is what was being discussed but I've decided to add some to this topic. I always thought the only stupid question was one that wasn't asked?? But I'm going to move sideways on the OP since this is so old.
This older thread, bumped now, brushes against an overall understanding of the aluminum boat market in the US and aluminum alloy boats in general. In this reply I’ll try to share my understanding of the metal as applied to boats and why the characteristics of the metal in different alloys and thicknesses have lead to what we see in our markets today. Just one more point of view (IMO) which I hope will add to the discussion of a topic this site is dedicated to address.
Both the alloy and thickness (composition and scantlings) of aluminum contribute to the engineering choice of methods used building a boat from any given combination of alloy and thickness metal. That may seem overly obvious but it’s pretty much the deciding factor in all our alum. boats. Building for profit, and profiting from that build, is the primary market-force determining which combination of aluminum’s many variables are chosen for the design to be built.
I’ll generalize to shorten my long post; thin scantling boats for inland waters primarily used for recreation (still a 'profit' in use) most often use alloys that lend themselves to stretch forming, press forming and other machine operations when compared to saltwater, longer LOA, larger displacement hulls which are primarily joined by welding. (MIG & TIG & soon some laser)
Formed boats have entire panels formed by various machine operations- so the entire half of a bottom or topsides panel, including longitudinal stiffeners are created in one operation prior to assembly on the hull. Welded boats, on the other hand are usually made of flat plates at least or greater than 1/8”/0.125” thick materials, where the outline of a hull panel is cutout flat then applied to a form, frame or just edge joined to the adjacent by ‘tacking’ up. Most welded plate boats incorporate only three geometric shapes in the hulls; flats, cylinders or conic sections and in a well designed and built example all three shapes blend into one another. Lighter wt, formed hulls can have more compound shapes incorporated as the topsides forward could be actually flared using a press formed panel. Rare is the welded boat under 40' with a flare in the bow instead of just flam.
Many welded plate boats are not built with jigs or fixtures as is more common with press formed riveted boats as the cost to build those frames/fixtures is prohibitive unless the goal is to produce a large number of identical hulls- something more often seen in manufactured boats with thinner scantlings.
All aluminum alloy sheets/plates become more stiff and ‘stronger’ (loosely used term here) when bent, rolled, pressed into a shape or stretched over a combination shape (forming die) with longitudinal ridges in the die. This stiffening and strengthening is planned into formed boats’ structure but is limited to specific alloys and then in thinner materials if compared to plate alloy hulls. These alloys are originally more ductile and less stiff but become very stiff and proportionally ‘stronger’ once formed into a cupped or curved panel with ‘longitudinal’ ribs/rails/rubbing strakes. That fact, seen in the bottoms and topsides of most formed boats is what allows their manufacture as we see in the Monarch, Bay Runner, Starcraft, Myers (sp?) and many other brands.
For the most part these boats are from 10-12’ to 20-some’, are very light for their LOA, and include pontoon boats and aluminum canoes. On the other hand most welded boats’ original materials are from the 5000 and 6000 series of aluminum alloys. These two alloy series have very good welding properties but must be formed with much (MUCH) greater radius of bends and are not used to ‘stretch form'. However, a few of the more ductile 5000 series (5052) can be roll formed; if care is taken with the tooling design. Most of the formed boats’ hull seams are riveted while most of those comparable seams in the plate alloy boats are welded.
I divided the aluminum boat market into two major categories based on the alloys and scantlings, which imply the primary hull panel joining methods; rivets vs welding. However, some manufacturers use welding in various seams of formed boats and once in a while you’ll see a hatch riveted onto a coaming to avoid heating thinner bent materials at a hinge point. In the main, 5k & 6k alloy boats are ‘plate’ as they typically use hull panels and framing elements of 1/8” and heavier; while that’s not the same for the lighter wt formed hulls.
Both hull groups benefit from aluminum extrusions. These are just specific shapes of (most often 6061 T-6 alloy) that have been forced through a very exactly shaped plate to result in a long uniform pipe shape, a T or and L or some more specifically complex shape used at the keel, chine or shear of a hull to help joint the two adjoining hull panels at that longitudinal seam. Where lighter hulls would have an extrusion combined with a gasket material and rivets to join the keel, chines or topsides at the shear- comparable extrusions would be welded to plate alloy boats in the same hull seams.
Obviously, there’s a lot more involved to cover the topic well.
I wanted to associate the metal’s various commercially supplied forms and its related chemical/physical properties to the two major vessel groups that have evolved and are sold today. If anyone had specific questions, or corrections and other observations please don’t hesitate to post up.
Cheers,
Kevin Morin
Kenai, AK.
This older thread, bumped now, brushes against an overall understanding of the aluminum boat market in the US and aluminum alloy boats in general. In this reply I’ll try to share my understanding of the metal as applied to boats and why the characteristics of the metal in different alloys and thicknesses have lead to what we see in our markets today. Just one more point of view (IMO) which I hope will add to the discussion of a topic this site is dedicated to address.
Both the alloy and thickness (composition and scantlings) of aluminum contribute to the engineering choice of methods used building a boat from any given combination of alloy and thickness metal. That may seem overly obvious but it’s pretty much the deciding factor in all our alum. boats. Building for profit, and profiting from that build, is the primary market-force determining which combination of aluminum’s many variables are chosen for the design to be built.
I’ll generalize to shorten my long post; thin scantling boats for inland waters primarily used for recreation (still a 'profit' in use) most often use alloys that lend themselves to stretch forming, press forming and other machine operations when compared to saltwater, longer LOA, larger displacement hulls which are primarily joined by welding. (MIG & TIG & soon some laser)
Formed boats have entire panels formed by various machine operations- so the entire half of a bottom or topsides panel, including longitudinal stiffeners are created in one operation prior to assembly on the hull. Welded boats, on the other hand are usually made of flat plates at least or greater than 1/8”/0.125” thick materials, where the outline of a hull panel is cutout flat then applied to a form, frame or just edge joined to the adjacent by ‘tacking’ up. Most welded plate boats incorporate only three geometric shapes in the hulls; flats, cylinders or conic sections and in a well designed and built example all three shapes blend into one another. Lighter wt, formed hulls can have more compound shapes incorporated as the topsides forward could be actually flared using a press formed panel. Rare is the welded boat under 40' with a flare in the bow instead of just flam.
Many welded plate boats are not built with jigs or fixtures as is more common with press formed riveted boats as the cost to build those frames/fixtures is prohibitive unless the goal is to produce a large number of identical hulls- something more often seen in manufactured boats with thinner scantlings.
All aluminum alloy sheets/plates become more stiff and ‘stronger’ (loosely used term here) when bent, rolled, pressed into a shape or stretched over a combination shape (forming die) with longitudinal ridges in the die. This stiffening and strengthening is planned into formed boats’ structure but is limited to specific alloys and then in thinner materials if compared to plate alloy hulls. These alloys are originally more ductile and less stiff but become very stiff and proportionally ‘stronger’ once formed into a cupped or curved panel with ‘longitudinal’ ribs/rails/rubbing strakes. That fact, seen in the bottoms and topsides of most formed boats is what allows their manufacture as we see in the Monarch, Bay Runner, Starcraft, Myers (sp?) and many other brands.
For the most part these boats are from 10-12’ to 20-some’, are very light for their LOA, and include pontoon boats and aluminum canoes. On the other hand most welded boats’ original materials are from the 5000 and 6000 series of aluminum alloys. These two alloy series have very good welding properties but must be formed with much (MUCH) greater radius of bends and are not used to ‘stretch form'. However, a few of the more ductile 5000 series (5052) can be roll formed; if care is taken with the tooling design. Most of the formed boats’ hull seams are riveted while most of those comparable seams in the plate alloy boats are welded.
I divided the aluminum boat market into two major categories based on the alloys and scantlings, which imply the primary hull panel joining methods; rivets vs welding. However, some manufacturers use welding in various seams of formed boats and once in a while you’ll see a hatch riveted onto a coaming to avoid heating thinner bent materials at a hinge point. In the main, 5k & 6k alloy boats are ‘plate’ as they typically use hull panels and framing elements of 1/8” and heavier; while that’s not the same for the lighter wt formed hulls.
Both hull groups benefit from aluminum extrusions. These are just specific shapes of (most often 6061 T-6 alloy) that have been forced through a very exactly shaped plate to result in a long uniform pipe shape, a T or and L or some more specifically complex shape used at the keel, chine or shear of a hull to help joint the two adjoining hull panels at that longitudinal seam. Where lighter hulls would have an extrusion combined with a gasket material and rivets to join the keel, chines or topsides at the shear- comparable extrusions would be welded to plate alloy boats in the same hull seams.
Obviously, there’s a lot more involved to cover the topic well.
I wanted to associate the metal’s various commercially supplied forms and its related chemical/physical properties to the two major vessel groups that have evolved and are sold today. If anyone had specific questions, or corrections and other observations please don’t hesitate to post up.
Cheers,
Kevin Morin
Kenai, AK.
Last edited by kmorin on Sat Feb 17, 2024 1:06 am, edited 1 time in total.
Reason: para's
Reason: para's
kmorin