Labor Hours
-
- Posts: 6
- Joined: Thu Nov 30, 2023 4:46 pm
Labor Hours
New to the board!
I have ordered a Specmar kit. It's their 4.5m rib (https://www.specmar.com/aluminum-boat-p ... r-rib-1334). I had planned to build it myself with a friend that is a MUCH more experienced welder (yes, aluminum). It's 3/8" keel and 3/16" for everything else.
I've gotten myself into projects before and completely underestimated the time it would take to finish. To try and keep the wife happy and not take half the garage up for XXX amount of time, I wanted to price out getting the welding done (I'd still rig it, install the tubes, and do the rest). I stopped by a locally recommended fab shop to see what they'd say - Let's just say I did a double take (The hourly rate was consistent with my expectations, the hours seemed high).
Scope: Welding only, from CNC cut/marked parts (I will cut everything out and deliver).
How many man hours should it take for an experienced fabricator?
I am try to attached a 110 kb file but it's not letting me - I will try again shortly.
Thanks!
I have ordered a Specmar kit. It's their 4.5m rib (https://www.specmar.com/aluminum-boat-p ... r-rib-1334). I had planned to build it myself with a friend that is a MUCH more experienced welder (yes, aluminum). It's 3/8" keel and 3/16" for everything else.
I've gotten myself into projects before and completely underestimated the time it would take to finish. To try and keep the wife happy and not take half the garage up for XXX amount of time, I wanted to price out getting the welding done (I'd still rig it, install the tubes, and do the rest). I stopped by a locally recommended fab shop to see what they'd say - Let's just say I did a double take (The hourly rate was consistent with my expectations, the hours seemed high).
Scope: Welding only, from CNC cut/marked parts (I will cut everything out and deliver).
How many man hours should it take for an experienced fabricator?
I am try to attached a 110 kb file but it's not letting me - I will try again shortly.
Thanks!
-
- Posts: 6
- Joined: Thu Nov 30, 2023 4:46 pm
Re: Labor Hours
Since I can't upload, this link should work:
https://postimg.cc/CRC1Y4Lv
The beam is 73 5/78"
Hull length is ~13'
https://postimg.cc/CRC1Y4Lv
The beam is 73 5/78"
Hull length is ~13'
- gandrfab
- Posts: 594
- Joined: Fri Mar 28, 2008 12:33 pm
- 16
- Your location: Edgewater Fl
- Location: Edgewater Fl
Re: Labor Hours
The theory that everything is going to fit (pop into place and go as planned) is almost never how it works out.
Maybe approach the task with a value cost and not a time cost.
Agree on a value of job complete and let the shop work out their hours.
Just an idea.
Maybe approach the task with a value cost and not a time cost.
Agree on a value of job complete and let the shop work out their hours.
Just an idea.
-
- Posts: 6
- Joined: Thu Nov 30, 2023 4:46 pm
Re: Labor Hours
Thanks for the reply
I agree, things don't always fit perfectly. I would have been ok with a fixed price number too.
But (since no one has any guesses), I throw it out there:
est. of 300 hours at $120/hr for a 13'6 hull (no sides or gunnels since it's a rib)
That could be high, that could be low. Either way, too rich for me. He was cool about it and said that he'd do piecemeal parts if I needed help. I'm going to use him for the few items that need bending on the brake press (I'll happily pay the $120/hr for that).
If it takes me longer to put it together myself, that's what it's going to take.
I agree, things don't always fit perfectly. I would have been ok with a fixed price number too.
But (since no one has any guesses), I throw it out there:
est. of 300 hours at $120/hr for a 13'6 hull (no sides or gunnels since it's a rib)
That could be high, that could be low. Either way, too rich for me. He was cool about it and said that he'd do piecemeal parts if I needed help. I'm going to use him for the few items that need bending on the brake press (I'll happily pay the $120/hr for that).
If it takes me longer to put it together myself, that's what it's going to take.
Re: Labor Hours
Won’t guess the hrs and certainly can’t call myself experienced however……
I took delivery last march of all the pieces from the CNC shop for Specmar’s Outback hull (16’ tunnel) and working on it on the weekends in my wife’s parking spot in the home garage it took me 6 months for me to get the the boat to stage for me to do a quick sea trial, that was just basically the main structure with the motor hung.
I’m now disassembling all the rigging to do the final finishing and minor fabrication of mounts and accessories.
So basically a year ( I could never make money at it and its way more work than I expected) working on it part time and lots of waiting on parts
Definitely a fun project I’m glad I did.
I took delivery last march of all the pieces from the CNC shop for Specmar’s Outback hull (16’ tunnel) and working on it on the weekends in my wife’s parking spot in the home garage it took me 6 months for me to get the the boat to stage for me to do a quick sea trial, that was just basically the main structure with the motor hung.
I’m now disassembling all the rigging to do the final finishing and minor fabrication of mounts and accessories.
So basically a year ( I could never make money at it and its way more work than I expected) working on it part time and lots of waiting on parts
Definitely a fun project I’m glad I did.
- welder
- Site Admin
- Posts: 4668
- Joined: Thu Jan 03, 2008 11:51 pm
- 16
- Location: Whitesboro, Texas
- Contact:
Re: Labor Hours

We would love to see some pictures of the build.


Lester,
PacificV2325, Honda BF225
2386
PacificV2325, Honda BF225
2386
-
- Posts: 6
- Joined: Thu Nov 30, 2023 4:46 pm
Re: Labor Hours
Thank you!Sr wrote:Thu Jan 01, 1970 9:10 am Won’t guess the hrs and certainly can’t call myself experienced however……
I took delivery last march of all the pieces from the CNC shop for Specmar’s Outback hull (16’ tunnel) and working on it on the weekends in my wife’s parking spot in the home garage it took me 6 months for me to get the the boat to stage for me to do a quick sea trial, that was just basically the main structure with the motor hung.
I’m now disassembling all the rigging to do the final finishing and minor fabrication of mounts and accessories.
So basically a year ( I could never make money at it and its way more work than I expected) working on it part time and lots of waiting on parts
Definitely a fun project I’m glad I did.
That's the type on information I was looking for. I am almost ready to start. Getting the space in the garage cleared has been a challenge in itself.
-
- Donator 08, 09, 10, 11, 12, 13, 14, 15, 16, 17, 18, 19, 20, 21, 22, 23, 24
- Posts: 1745
- Joined: Mon Aug 18, 2008 1:37 am
- 15
- Your location: Kenai, AK
- Location: Kenai, Alaska
Re: Labor Hours
starbright, Welcome to the AAB.com Forum, as welder has mentioned, build sequence image posts are always widely read here, hope you'll share yours?
My primary problem with trying to realistically predict the man-hours to complete a little pre-cut skiff-kit is the “unknowable” differences between first time builders’ skills and associated metal working experiences which will lengthen or shorten the work effort required.
I have built lots of welded aluminum boats; in lengths from a few feet LOA to 42 feet, including a 50’ steel inshore crabber in the 1970’s using stick rod and cut-out by hand with O/A! The (vast) number of mistakes I made (or as some might call them “the accumulated experiences of building in welded metal over hundreds of boats”) all contributed to reduced man-hours of effort and better quality projects the longer I kept building.
While remembering my mistakes and trying to avoid them in the next build reduced hours - repeating them by not understanding what went wrong; lengthened the hours in the next build. So, I’d never try to estimate first skiff hours as there may well be 10x difference in total from builder to builder.
I haven’t posted before because I don’t see how anyone’s first build could be predicted with any accuracy? My advice (and I know you won’t take it) is: (#1) practice MIG welding for 100 hours BEFORE you light up on your boat. And, to practice TIG for 100 hours as well. (#2) Learn to ‘break/bend’ or weld test your practice coupons so you can find the smallest but still strong enough bead to use in all weld joints and stick with those results.
90% of “misfit parts” (IME) from NC cut skiffs seem to me, caused by new builders’ lack of discipline/methodology/tradecraft in tack and weld size, final weld sequence (weld schedule) and lack of skill and awareness while applying appropriately planned beads to assemble and weld-out the boat.
Please don’t take offense at a report of the lessons from many years of experience trying to learn to build welded aluminum boats and observing others’ progress to that goal.
Good luck with your project. I don't think the total man-hours matter? I hope your first skiff isn’t your last, and the new boat gives you many hours of enjoyment that can only be enjoyed in a certain way by those building their own boat.
Cheers,
Kevin Morin
Kenai, AK
My primary problem with trying to realistically predict the man-hours to complete a little pre-cut skiff-kit is the “unknowable” differences between first time builders’ skills and associated metal working experiences which will lengthen or shorten the work effort required.
I have built lots of welded aluminum boats; in lengths from a few feet LOA to 42 feet, including a 50’ steel inshore crabber in the 1970’s using stick rod and cut-out by hand with O/A! The (vast) number of mistakes I made (or as some might call them “the accumulated experiences of building in welded metal over hundreds of boats”) all contributed to reduced man-hours of effort and better quality projects the longer I kept building.
While remembering my mistakes and trying to avoid them in the next build reduced hours - repeating them by not understanding what went wrong; lengthened the hours in the next build. So, I’d never try to estimate first skiff hours as there may well be 10x difference in total from builder to builder.
I haven’t posted before because I don’t see how anyone’s first build could be predicted with any accuracy? My advice (and I know you won’t take it) is: (#1) practice MIG welding for 100 hours BEFORE you light up on your boat. And, to practice TIG for 100 hours as well. (#2) Learn to ‘break/bend’ or weld test your practice coupons so you can find the smallest but still strong enough bead to use in all weld joints and stick with those results.
90% of “misfit parts” (IME) from NC cut skiffs seem to me, caused by new builders’ lack of discipline/methodology/tradecraft in tack and weld size, final weld sequence (weld schedule) and lack of skill and awareness while applying appropriately planned beads to assemble and weld-out the boat.
Please don’t take offense at a report of the lessons from many years of experience trying to learn to build welded aluminum boats and observing others’ progress to that goal.
Good luck with your project. I don't think the total man-hours matter? I hope your first skiff isn’t your last, and the new boat gives you many hours of enjoyment that can only be enjoyed in a certain way by those building their own boat.
Cheers,
Kevin Morin
Kenai, AK
Last edited by kmorin on Tue Jan 23, 2024 3:11 pm, edited 1 time in total.
Reason: paragraphs
Reason: paragraphs
kmorin
Re: Labor Hours
Building a kit is a learning experience. It will save you money on a boat if you consider your learning time an investment. I didnt get paid to go to college, not sure about you... Learn the skills, do the best you can, and enjoy the process. If you do it well, you will be damned proud of that boat when it hits the water, and might start thinking about the next one. What you have taken on isn't easy, but could be very rewarding.
-
- Posts: 6
- Joined: Thu Nov 30, 2023 4:46 pm
Re: Labor Hours
Thanks Kevin - somehow I missed your reply earlier. I understand there are so many variables that it would hard to completely quantify. I guess it was just the initial shock of a professional fabrication shop telling me it would take them 300 hours. I would have taken anyone's estimate and then doubled it since I'm new to it!kmorin wrote: ↑Tue Jan 23, 2024 3:09 pm starbright, Welcome to the AAB.com Forum, as welder has mentioned, build sequence image posts are always widely read here, hope you'll share yours?
My primary problem with trying to realistically predict the man-hours to complete a little pre-cut skiff-kit is the “unknowable” differences between first time builders’ skills and associated metal working experiences which will lengthen or shorten the work effort required.
I have built lots of welded aluminum boats; in lengths from a few feet LOA to 42 feet, including a 50’ steel inshore crabber in the 1970’s using stick rod and cut-out by hand with O/A! The (vast) number of mistakes I made (or as some might call them “the accumulated experiences of building in welded metal over hundreds of boats”) all contributed to reduced man-hours of effort and better quality projects the longer I kept building.
While remembering my mistakes and trying to avoid them in the next build reduced hours - repeating them by not understanding what went wrong; lengthened the hours in the next build. So, I’d never try to estimate first skiff hours as there may well be 10x difference in total from builder to builder.
I haven’t posted before because I don’t see how anyone’s first build could be predicted with any accuracy? My advice (and I know you won’t take it) is: (#1) practice MIG welding for 100 hours BEFORE you light up on your boat. And, to practice TIG for 100 hours as well. (#2) Learn to ‘break/bend’ or weld test your practice coupons so you can find the smallest but still strong enough bead to use in all weld joints and stick with those results.
90% of “misfit parts” (IME) from NC cut skiffs seem to me, caused by new builders’ lack of discipline/methodology/tradecraft in tack and weld size, final weld sequence (weld schedule) and lack of skill and awareness while applying appropriately planned beads to assemble and weld-out the boat.
Please don’t take offense at a report of the lessons from many years of experience trying to learn to build welded aluminum boats and observing others’ progress to that goal.
Good luck with your project. I don't think the total man-hours matter? I hope your first skiff isn’t your last, and the new boat gives you many hours of enjoyment that can only be enjoyed in a certain way by those building their own boat.
Cheers,
Kevin Morin
Kenai, AK
Thank you for all your write ups - I think the Glen L write ups are the most comprehensive that I've found so far.
I have started playing around with my machine. This was day #1. I still need to figure out travel speed better as it always starts cold and ends up hot (and will need to play with the hot start functions and crater fill options) and play with gas as I still get a lot of "soot" around the weld itself.
I agree with you, I will probably not listen to you and MIG for 100 hours before starting - I think I will run out of aluminum scrap long before then!!! I have been doing destruction testing on my practice pieces haven't gotten anything to break yet. I DO need to get things prettier though before I start using the real thing.
Double pulse (meaning that wasn't me manipulating the gun) on 3/16" with 0.035" 5356:
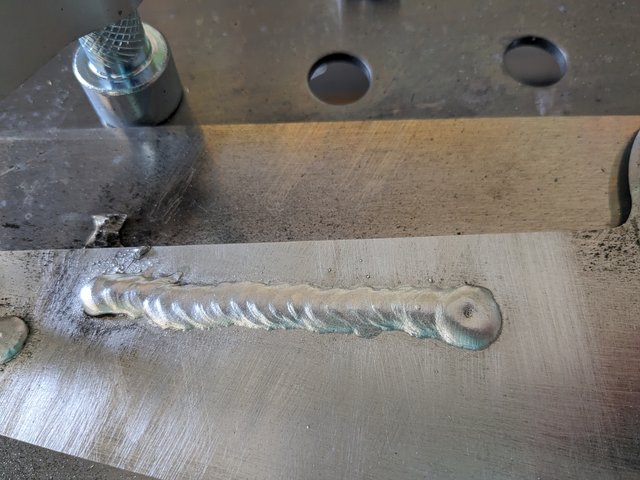
I will have to butt weld the keel together - it's in two pieces. I wanted to see how I could do with 0.030" even though the machine says max of 1/4" on it with 0/030". The machine says I needs 3/64" wire to do 3/8".
First pass, no beveling, no preheat , no pulse, straight spray, with 0.030" on 3/8":
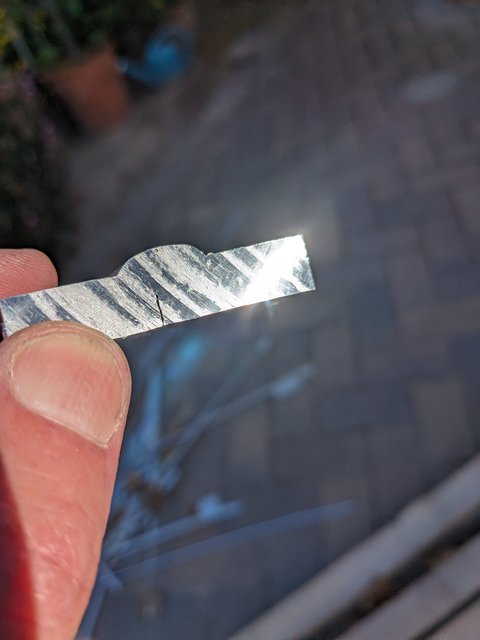
With a second pass on the other side, same parameters:
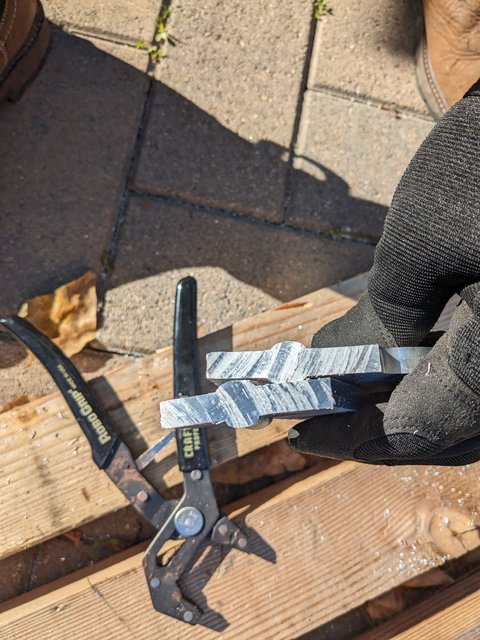
I think I was able to get full penetration here. I didn't put Easy-Off on it to etch it but there's no way that's coming apart!